Our Group Home has moved. Please visit our Group Website for other Business Lines and Country Sites.
Custom Counterweights in Cast Iron: Rapid Turnaround Case Study
In the fast-paced world of industrial manufacturing, delivering high-quality casting products on a tight schedule can be challenging. In our latest post, we share an insightful case study that demonstrates our ability to meet and exceed customer expectations. Discover how Exxelmet successfully delivered Custom Counterweights made of Cast Iron for a major project in record time. #CastIronCounterweights #EnergyEfficiency #Sustainablility #Manufacturing #CastIron #CustomCounterweights #RapidTurnaround #Engineering
COUNTERWEIGHT
Rupesh Madhogaria
7/2/20242 min read
Case Study: Rapid Turnaround in Delivering Custom Counterweights in Cast Iron
Overview
In the competitive industrial products sector, a leading manufacturer faced a challenge from a major company needing custom counterweights made of cast iron. This case study highlights how Exxelmet efficiently managed the process from initial design to pattern making and delivery, achieving an impressively quick turnaround time that exceeded the customer’s expectations.
The Challenge
A large company embarked on a large-scale project requiring custom counterweights made of cast iron for their heavy machinery. These counterweights were essential for the safe and effective operation of cranes and other lifting equipment. The project had a tight deadline, and delays could lead to significant financial losses and project setbacks.
The specific requirements were:
Unique counterweight design specifications to fit new machinery.
High precision and quality standards for castings.
A strict deadline of eight weeks from design approval to final delivery.
Strategy and Execution
To meet the stringent requirements and tight deadline, Exxelmet implemented a multi-phase strategy focusing on efficiency and coordination across all stages:
Initial Design and Consultation for Cast Iron Counterweight
Rapid Needs Assessment: Within the first two days, a dedicated team met with the customer company to understand their specific needs and constraints.
Design Proposal: Leveraging advanced software, the team developed a detailed design proposal in three days, incorporating all the necessary specifications and safety standards.
Cast Iron Counterweight Pattern Making and Prototyping
Concurrent Engineering: While the design was being finalized, the pattern-making team began preparing cast iron counterweight pattern materials and tools, allowing for immediate transition once the counterweight design was approved.
Prototype Development: A cast iron counterweight prototype was produced within five days for initial validation and fitment checks. This rapid prototyping of the cast iron counterweight ensured any design flaws were identified and corrected early.
Cast Iron Counterweight Production and Quality Control
Streamlined Manufacturing Process: The production phase began immediately after the cast iron counterweight prototype was approved, and counterweights were manufactured with high precision and weight tolerance.
Quality Assurance: Throughout the production process, rigorous quality control checks were performed to ensure the counterweights met all specifications and industry standards.
Logistics and Delivery
Optimized Logistics: Simultaneously, the logistics team coordinated with suppliers and transportation services to ensure a seamless supply chain. A just-in-time inventory approach was adopted to minimize delays.
Timely Delivery: The final products were dispatched to the construction site within three days after production completion, well within the eight-week deadline.
Results
Total Turnaround Time: 52 days from initial consultation to final delivery.
Customer Satisfaction: The customer was highly satisfied with the product quality and the adherence to the tight schedule. This efficiency not only prevented project delays but also enhanced the safety and performance of their machinery.
Business Impact: The success of this project reinforced the Exxelmet’s reputation for reliability and efficiency, leading to additional contracts and strengthened customer relationships.
Key Takeaways
Effective Communication: Regular updates and open communication channels between Exxelmet and the customer ensured that all requirements were clearly understood and met.
Advanced Technology: Utilizing rapid prototyping approach significantly shortened the design and validation phases.
Integrated Teams: Coordination between design, production, and logistics teams enabled parallel processing and reduced overall turnaround time.
Proactive Quality Control: Continuous quality checks throughout the production process prevented delays caused by potential defects or rework.
By adopting a strategic and well-coordinated approach, Exxelmet successfully delivered high-quality custom cast iron counterweights within a very tight timeframe.
This case study exemplifies how Exxelmet can achieve rapid turnaround times through efficiency and teamwork.
For additional information on our cast iron counterweights and how they can benefit your specific application, get in touch with us on contact@exxelmet.com, or fill up the contact form
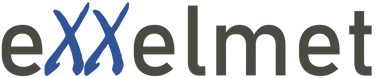
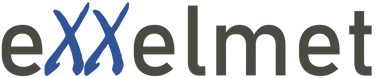
Copyright © 2025 Exxelmet
P-200, Benares Road, P. O. Netajigarh, Howrah, West Bengal, India. Pin Code 711108
Tel: +91 98311 11541
Email: contact@exxelmet.com